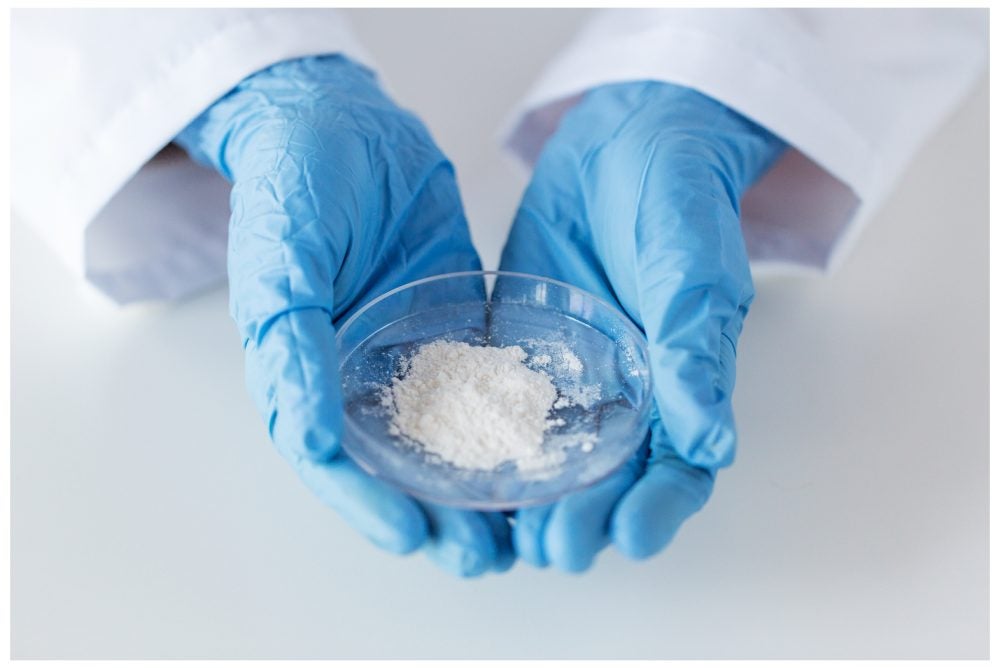
Demand for APIs and other high-potency drugs are increasing[i].
The manufacturing of these products takes place in high containment facilities, using premium, specialised equipment that separates operators from materials and safeguards personnel from exposure and cross-contamination.
For millers, it is critical to comply with regulatory standards for good manufacturing practices (GMP) and quality control to ensure safety, uniformity, reproducibility, and product quality, with the milling process properly validated and documented.
But most pharma manufacturers have limited in-house facilities, and this is bringing to the forefront third-party pharmaceutical mill providers, more often called contract manufacturers (CMO’s), and their capabilities.
Why is rising API production so important?
A recent report by GlobalData, Contract Small Molecule API Manufacturing Industry by the Numbers[ii], analysed 2,787 small molecule API contract manufacturing facilities. Of those, only 935 (34%) offered containment capabilities, while only 256 facilities (9%) offered controlled substance capabilities.
Demand for APIs is particularly high, and likely to remain so, especially with the increase in new molecular entities (NMEs) requiring special handling, such as oncology kinase inhibitor drug approvals and antibody drug conjugates, as well as cytotoxics.
This means that operators with greater manufacturing flexibility and a broader range of specialised capabilities are more likely to succeed in adapting to the changing API landscape. Consequentially, the increasing complexity of small molecule APIs will benefit manufacturers that have specialised containment and controlled substance capabilities.
The benefits of high-impact milling
High-impact milling of APIs can help achieve a more uniform particle size distribution, ensuring more consistent drug delivery and dosage, and this ability to finely control particle size can facilitate the development of novel drug delivery systems and formulations.
Micronization is a form of fine size milling, which reduces the particle size of APIs, enhancing their dissolution rate and improving bioavailability, leading to better therapeutic outcomes. Micronization can also contribute to cost optimisation by improving the efficiency of drug manufacturing processes and reducing the amount of API required in formulations.
The choice of milling method and equipment depends on several key factors, including the desired particle size, the characteristics of the material being milled and the specific requirements of the formulation or process.
Current methods include ball, hammer, pin and disc mills. However, these techniques frequently produce loud noise levels and high process temperatures, which can be dangerous for workers. Furthermore, overheating a product can shorten its shelf life, reduce its effectiveness, and increase the risk of an explosion.
High-impact milling safety challenges
Working with highly toxic and combustible materials presents some unique safety challenges for manufacturers. Many pharmacological ingredients are highly potent, even in micro-gram quantities and represent a risk to human health as well as cross-contamination with other drugs in a manufacturing setting.
Four key safety challenges that need to be addressed by millers are:
- Hazardous substances: High-impact milling may involve the handling and processing of highly potent drug compounds or other hazardous substances. Ensuring proper containment of these substances is crucial to prevent cross-contamination and exposure to workers and the environment.
- Dust explosion risk: The creation of fine particles can pose a risk of dust explosions if not properly controlled. Using isolators or purging the milling equipment with inert gases like nitrogen can help to minimise the risk. Further, European ATEX Directive 2014/34/EU compliance[iii] regulates equipment and protective systems for use in potentially explosive atmospheres. Assessing explosion risks, applying protective measures, employing certified equipment, and teaching staff about potential explosion dangers and procedures are all part of ATEX compliance.
- Fire hazards: Certain materials used in high-impact milling processes, such as solvents or reactive compounds, can increase the risk of fire if not handled properly. Implementing measures such as proper ventilation, fire-detection systems and fire-suppression systems can help to mitigate this risk.
- Process safety incidents: Milling operations can be susceptible to process safety incidents, such as equipment malfunctions or technical defects, which can lead to leaks, explosions, or fires. Implementing robust process safety management systems and conducting risk assessments can help to identify and mitigate potential hazards.
By using new technologies, alongside traditional safety measures such as risk assessments, PPE (personal protective equipment) and thorough training, manufacturers can ensure they keep their operators safe.
Containment solutions
Frewitt is a world leader in powder size-reduction technology, and it offers a range of innovative solutions and cutting-edge products.
To prevent contamination, Frewitt has introduced a new module that improves machine cleaning, flow controls and overall stability in the milling process. The Profi-Sample uses an inflatable gasket in its design, which guarantees the protective containment seal between the grinding chamber and the sample chamber. The Profi-Sample allows for the taking of samples without interrupting the process.
In conjunction with a flow of air or nitrogen being injected precisely into the space between the sampling spoon and the frame, this allows two elements to remain clean and prevents them from becoming blocked, avoiding powder intrusions.
When it comes to eliminating combustion risks, the key is to implement milling technologies that achieve the highest levels of process efficiency while simultaneously providing an appropriate level of safety for workers operating the milling machines.
Frewitt’s latest patented development, the Power Mill PMV-320, is a single system that combines containment and micronization processes in a unique, patented process, which maintains a vacuum environment, ensuring both product and operator safety.
Because air, and consequentially, oxygen, is reduced in the system below the level of combustion, Frewitt’s process removes traditional risks such as explosion, while reduced friction results in less heating of the product, protecting molecular stability, therefore preserving its bio-performance.
The mill operates in a vacuum and is completely contained, with particles being processed in a negative atmosphere, material cannot exit the system. Frewitt’s vacuum cycle is controlled using pressure sensors, ensuring a constant vacuum condition.
Additionally, a temperature measurement sensor, fully compatible with Frewitt systems, functions as a redundancy measure that detects overheating and shuts down milling machinery in the highly improbable event that the temperature threshold is exceeded.
For more information, download the paper below.
[i] [ii] GlobalData: Contract Small Molecule API Manufacturing Industry by the Numbers – 2021 Edition:
https://pharma1.globaldata.com/Analysis/TableOfContents/Contract-Small-Molecule-API-Manufacturing-Industry-by-the-Numbers—2021-Edition
[iii] https://single-market-economy.ec.europa.eu/sectors/mechanical-engineering/equipment-potentially-explosive-atmospheres-atex_en