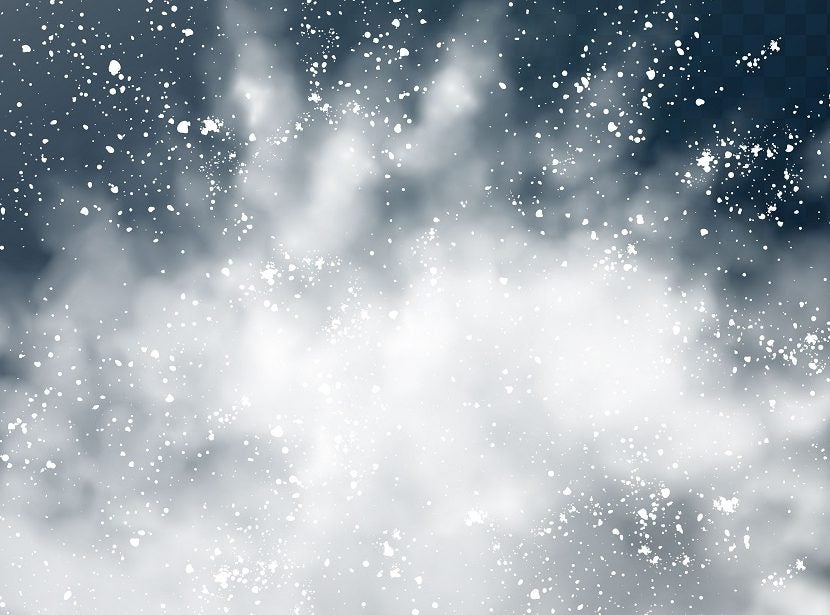
When it comes to milling drug products, the energy and time taken are major cost factors for the miller. But the innovative process of cryo-milling, or cryogenic milling, offers a safe and effective alternative to standard milling techniques.
Cryo-milling involves freezing a material in liquid nitrogen (-100°C to -150°C) before milling or milling the material under cryogenic conditions with liquid nitrogen present. Exposure to liquid nitrogen results in the ‘embrittlement’ of the material, which promotes the friability of the crystalline structure, lowering the kinetic energy required for milling, which can reduce time and costs.
The process’ physical properties limit degradation, preserving the quality of the milled product, as the material is less likely to heat, soften, and consequentially clog up screens or filters.
Notably, the similar process of freeze drying (lyophilization) is more suitable for liquids or solids having a higher residual moisture content, but cryo-milling suits materials that are soft, elastic/plastic, non-brittle and sensitive to temperature-induced changes (thermolabile).
Cryo-milling and pharma
Despite the ability of cryo-milling to produce both ultra-fine micron size particles, until recently it was not widely adopted in the pharmaceutical industry for the milling of drugs.
However, ten years ago, researchers used the methodi to mill phenytoin and polyvinylpyrrolidone to improve the dissolution rate of the drug, which is critical to the therapeutic efficacy of certain medicinal products. The use of liquid nitrogen was found to prevent plastic deformation and improved the particle fracture process.
It is now known that cryo-milling can minimise the degradation of thermolabile drug substances and the loss of volatile compounds. It also reduces the risk of explosion, oxidation of formulation constituents, and helps to inhibit particle agglomeration during milling.
As cryo-milling decreases the effect of temperature-induced changes during the milling process, studies have shown that co-grinding drugs and excipients under cryogenic conditions prevents the melt phase and leads to higher levels of amorphization.
This makes cryogenic milling advantageous as it enables the production of amorphous material without the negative effects of solvents or heating.
Why choose cryo-milling?
Cryo-milling offers numerous benefits for pharmaceutical products. For instance, homogeneity is crucial for producing drug-delivery devices with high-potency drugs. By homogenising low-concentration active pharmaceutical ingredients (APIs) into a polymer, cryo-milling can increase the surface area, making it easier to distribute the drugs evenly.
For high-potency drugs or controlled substances, additional safety measures are necessary to prevent harmful exposure to operators and the environment. However, with cryo-milling it is possible to dose the powdered polymer and pharmaceutical drug blend in a closed system in one feed stream, reducing the need for additional safety controls.
Cryo-milling also enhances flowability, as polymer beads and drug powders are often in pellet form. The process breaks down the polymer, enhancing mixture flow and allowing for easier feeding into an extruder. It also ensures temperature control, preventing polymer degradation or decomposition in high-energy environments.
Another benefit is accurate particle size distribution (PSD), which is particularly important for regulatory compliance as it may have an impact on the product’s effectiveness and/or shelf life.
Finally, cryo-milling promotes uniform shattering, which is crucial for drug-delivery devices, making this a highly effective technique.
Frewitt Cryo-Feeder CF-25
Frewitt is a Switzerland-based manufacturer of premium-quality mills and a world leader in powder size-reduction technologies. After analysing market requirements, the company has developed an innovative cryo-milling system that allows materials to be cooled to their point of friability to facilitate a mechanical reduction in a contained setting.
The Cryo-Feeder CF-25 features a modular form to flash-freeze products to the point of brittleness, allowing the conditioning of products that cannot be milled conventionally or are sensitive to a rise in temperature.
Features include:
- Automatic regulation of the liquid nitrogen supply to guarantee the immersion of the product at -196°C.
- Management of nitrogen consumption obtained by automated and secure control.
- Thermal insulation to prevent nitrogen evaporation and increase operator safety.
- Maximum size of the product at the entrance: 6mm.
- Product density of up to 2kg/dm3.
The system is designed to optimise production times and increase grinding quality, and its modular design ensures compatibility with the entire range of Frewitt machines, allowing for adaptation to future process requirements.
Cryo-milling is still a relatively new process, but one that offers a safe, optimised investment with anticipation of future needs as new drug products are developed. Other uses for cryo-milling and grinding are currently being examined, with scientists focusing on biopolymers as potential alternatives to synthetic plastics.ii
For further information on how Frewitt can help you with your project, download the paper below.